RepairMate: When Machines Break and Manuals Disappear
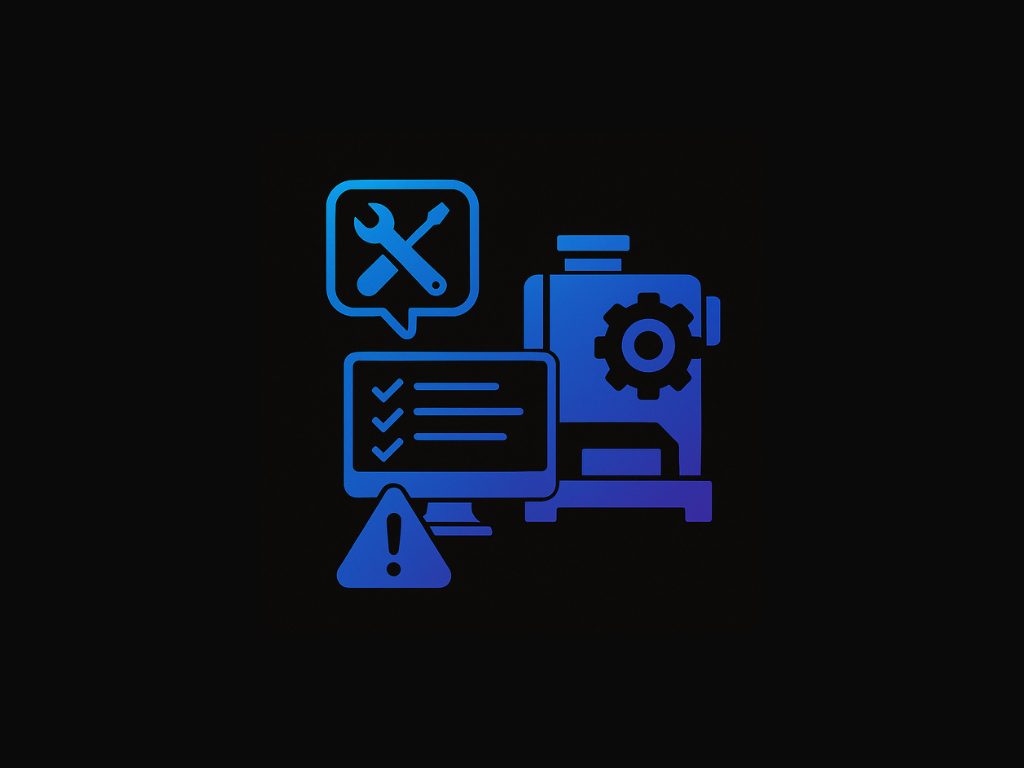
Have you ever been in that frustrating situation where a critical piece of equipment decides to stop working at the worst possible moment? And of course, the manual is nowhere to be found (or buried in a 300-page PDF that takes forever to search through).
That's exactly what happened to me repeatedly in my work as a medical technologist in a busy clinical laboratory.
The Lightbulb Moment
One particularly hectic day, our main chemistry analyzer broke down in the middle of processing urgent samples. The error message was cryptic, and the manual was... well, let's just say it wasn't where it should have been. After an hour of frantic searching and calls to colleagues, I finally found the solution to what turned out to be a simple fix.
That's when it hit me: "There has to be a better way to troubleshoot equipment issues."
Most laboratories and technical environments face the same challenge - we have multiple machines from different manufacturers, each with their own quirks, error codes, and maintenance procedures. When something goes wrong, the knowledge to fix it is often:
Hidden in massive technical manuals
Scattered across different documents
Known only to specific technicians who might not be available
Based on tribal knowledge that isn't properly documented
Building RepairMate
That frustration sparked the idea for RepairMate - a software solution designed to make troubleshooting equipment issues faster and more efficient. The concept is simple but powerful:
Create a central repository for all your equipment information
Document common issues with clear, step-by-step solutions
Allow troubleshooting by describing problems in plain language
Store manuals where they can be easily accessed
Build a knowledge base that grows with each resolved issue
How It Works
When a machine breaks down, you simply describe the problem you're experiencing in everyday language. RepairMate analyzes your description and matches it against known issues for that specific equipment.
It then presents the most likely solutions, with guided troubleshooting steps that anyone can follow. No need to memorize error codes or dig through manuals - just practical solutions when you need them most.
Beyond the Laboratory
While RepairMate was born from my experiences in the clinical laboratory, it's designed to help anywhere equipment maintenance is a challenge - manufacturing facilities, research labs, educational institutions, and more.
The goal is simple: reduce downtime, empower more people to solve technical problems, and create a system that gets smarter with every issue it helps resolve.
Looking Forward
RepairMate is still evolving, but I'm excited about its potential to transform how we handle equipment troubleshooting. No more hunting for manuals, calling around for the "guru" who knows that particular machine, or losing hours to avoidable downtime.
Instead, we can put solutions at everyone's fingertips and get back to the work that actually matters.
Have you faced similar challenges with equipment maintenance? I'd love to hear your experiences and thoughts on how we can make troubleshooting even more efficient.